A Manufacturing ERP acts as the central nervous system of your operation. It streamlines production workflows, optimizes processes, and empowers data-driven decisions that maximize profitability.
Explore this page to learn about the essential features of a Manufacturing ERP and gain a comprehensive insight into how it strengthens your business.
What is a manufacturing ERP and why do you need it?
WHAT IS A MANUFACTURING ERP SYSTEM?
Imagine a centralized hub that integrates every facet of your manufacturing process. That’s the essence of a Manufacturing ERP.
A comprehensive software solution designed to streamline and optimize your manufacturing operations—from planning and procurement to production, inventory management, and customer service.
By unifying data across various departments, a Manufacturing ERP fosters transparency, eliminates information silos, and empowers data-driven decision-making.
WHEN TO CONSIDER A MANUFACTURIG ERP SYSTEM?
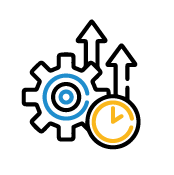
INEFFICIENT PROCESSES AND SILOS
Manufacturing businesses often rely on a complex web of manual processes, spread across different departments. This patchwork approach leads to inefficiencies and information gaps.
Data silos, where critical information is locked away in separate systems or departments, create blind spots that hinder visibility into production processes.
The combination of manual processes and data silos makes it difficult to identify and eliminate bottlenecks that slow down production.
INVENTORY MANAGEMENT CHALLENGES
Inventory management is a constant tightrope walk for manufacturers. Stumbling on either side can lead to significant financial management headaches. Here’s how:
- Stockouts: Running out of key raw materials or finished goods can bring production to a screeching halt. This not only delays deliveries but also damages customer relationships.
- Excess inventory: Holding onto too much inventory ties up valuable cash flow. It also increases storage costs and risks obsolescence, especially for products with short shelf lives or those susceptible to rapid technological advancements.
LIMITED PRODUCTION PLANNING AND SCHEDULING
Manufacturing in the dark, without a clear view of production realities, is like driving blindfolded down a winding road.
Fluctuating demand can throw a wrench into the best-laid plans, requiring adjustments to production schedules on the fly. Limited resources, such as skilled labor or specialized equipment, can create bottlenecks that stall production. Inefficient changeovers between different production runs further exacerbate the problem, wasting valuable production time.
These factors combined make it difficult to create and adhere to accurate production schedules, leading to delays, missed deadlines, and frustrated customers.
QUALITY CONTROL CONCERNS
Relying solely on manual inspections creates inconsistency in quality control. Inspectors can miss defects due to fatigue, subjectivity, or simply human error.
Additionally, limited visibility into the production process makes it difficult to identify where quality issues are arising. This lack of oversight can lead to defective products slipping through the cracks, resulting in a domino effect of problems.
SCALABILITY AND GROWTH CONSTRAINTS
As your business scales, the limitations of manual processes and disconnected systems become more apparent. An ERP system can help you manage this growth effectively by automating tasks, improving visibility, and fostering better collaboration.
INDUSTRY 4.0 READINESS
Disjointed communication and collaboration between departments create inefficiencies and missed opportunities.
Imagine a manufacturing company where departments operate in isolation. Production doesn’t have a clear picture of what sales are promising to customers. Changes in engineering are not communicated well to the shop floor, causing confusion and extra work.
This lack of collaboration creates inefficiencies, delays production, and hinders the company’s ability to adapt to market changes.
CORE FEATURES
These functionalities form the backbone of a Manufacturing ERP, providing the essential tools to manage production processes:
Multi-Level Bill of Materials (BOM)
Defines the components and quantities needed to produce a finished good.
Inventory Management
Maintains optimal stock levels and eliminates stockouts or overstocking. Tracks raw materials, work-in-progress (WIP), and finished goods efficiently.
Quality Control (QC)
Manages quality inspections, tracks defects, and ensures product consistency.
Real-Time Data Analytics
Offers deeper insights from production data. Leverages real-time data to identify trends, optimize production processes, and make data-driven decisions for continuous improvement.
Shop Floor Control
Provides production personnel with real-time access to work orders, manages inventory levels, and production instructions. Shop floor terminals foster process efficiency and data accuracy.
After-Sales Service
Integrates with Customer Relationship Management (CRM) systems to track customer inquiries, manage warranty claims, and provide efficient after-sales service, fostering long-term customer relationships.
Material Requirements Planning (MRP)
Calculates the specific quantities and timing of raw materials and components needed for production based on BOM and Master Production Schedule (MPS) data.
Production Planning & Scheduling
Provides real-time visibility into production capacity and material availability. Creates realistic production schedules that optimize resource allocation and ensure on-time deliveries.
Machine Learning & Predictive Maintenance
Analyzes equipment data and predicts potential failures using Machine Learning, allowing for proactive maintenance scheduling and minimized downtime.
Industrial Automation Systems Integration
Connects your ERP seamlessly to the shop floor. Enables real-time data exchange between machines and the ERP, fostering a more automated and efficient production environment.
ADVANCED FEATURES
Master Production Schedule (MPS)
Plans for future demand with accuracy. Creates a Master Production Schedule based on anticipated demand fluctuations, ensuring you have the right materials on hand to meet customer needs.
Capable to Promise (CTP)
Quotes realistic lead times with confidence. Analyzes production capacity and material availability to provide accurate delivery estimates to customers.
Advanced Planning and Scheduling (APS)
Leverages data-driven algorithms to create optimized production schedules, ensuring efficient resource utilization and timely deliveries.
Computerized Maintenance Management System (CMMS)
Prevents downtime and ensures machine health. Schedules proactive maintenance to reduce the risk of equipment failures and production disruptions.
Bill of Material Versions
Manages complex product structures with ease. Tracks components and sub-assemblies across multiple revisions, ensuring accurate production planning.
Configurator
Provides customized product offerings. Allows customers’ personalization of orders by selecting various options and features, boosting customer satisfaction and product differentiation.
Subcontracting
Extends production capabilities. Manages subcontractor network seamlessly, streamlining communication and ensuring timely delivery of outsourced components.
HOW A MANUFACTURING ERP CAN ADAPT TO DIFFERENT PRODUCTION PROCESSES
Here’s how a Manufacturing ERP caters to the distinct requirements of different production models.
CUSTOMER REQUIREMENTS
- Customization: The system allows for product personalization based on customer needs, generating unique production plans.
- Accurate lead times: Real-time data analysis ensures customers receive accurate estimates for their customized orders.
- Dynamic scheduling: Production schedules are optimized to handle a mix of custom orders, ensuring efficient resource allocation and timely deliveries.
- Project management: Integrated project management tools may be included for complex projects, facilitating task tracking, resource allocation, and cost control for each order.
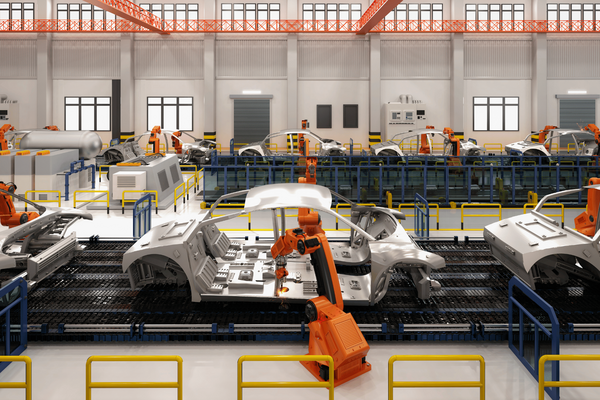
ANTICIPATED DEMAND
- Production planning: The system creates a master production schedule based on forecasts and historical data, ensuring adequate finished goods stock to meet anticipated demand.
- Material management: Features calculate precise material requirements based on production plans and product structures, ensuring timely procurement and avoiding stockouts.
- Inventory optimization: Robust tools help optimize stock levels, minimize carrying costs, and prevent overstocking.
- Demand forecasting: Advanced forecasting tools might be integrated to improve demand predictions and optimize production planning for anticipated needs.
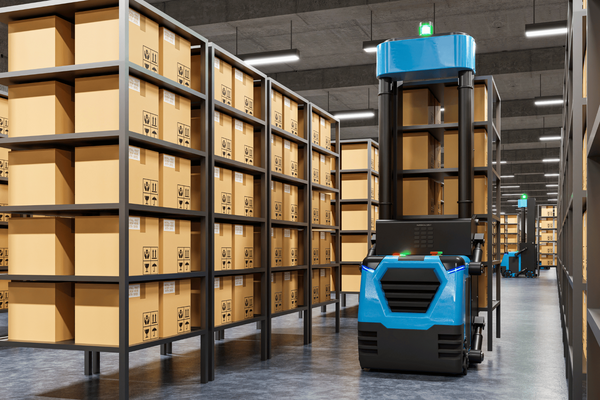
HIGHLY COMPLEX PRODUCTS
- Advanced project management: The system offers functionalities for managing complex engineering and manufacturing processes for unique products.
- Change order management: The system facilitates efficient handling of design changes and revisions during the engineering and production phases.
- CAD/CAM integration: Seamless data exchange between design software and the ERP ensures smooth project execution.
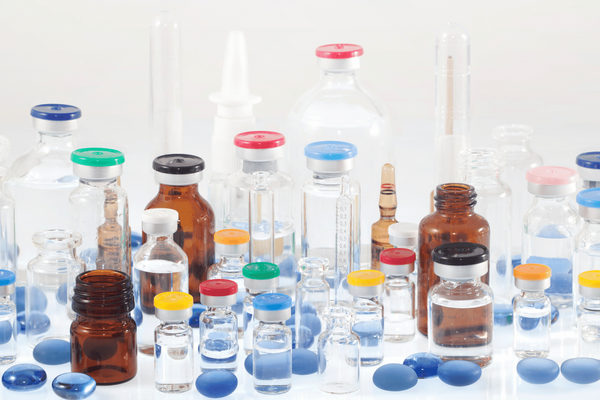
ASSEMBLED PRODUCTS
- Customization: The system allows customers to select preconfigured options for assembly.
- Kitting: Functionality enables efficient pre-assembly of standard component kits based on anticipated customer orders.
- Real-time inventory visibility: The system provides real-time insight into component stock levels to ensure smooth assembly operations.
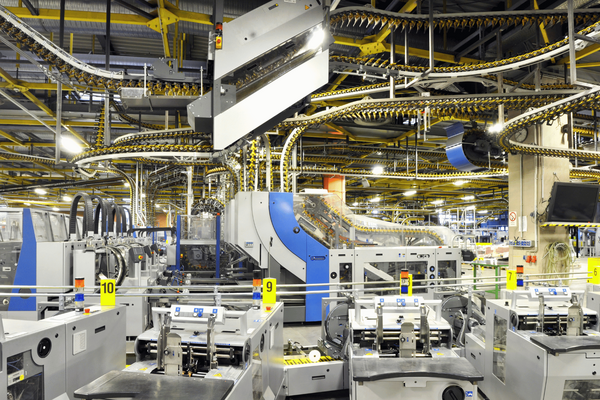
BEYOND SPECIFIC MODELS
Manufacturing ERPs can also cater to hybrid models that combine elements of different approaches depending on the product mix and customer demand. Additionally, subcontracting management and real-time shop floor control can enhance production flexibility and efficiency across diverse manufacturing environments.
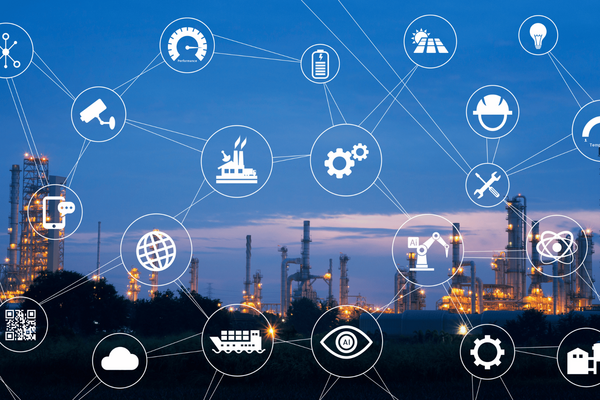
HOW TO SELECT THE BEST MANUFACTURING ERP FOR YOUR BUSINESS
In the complex landscape of intricate manufacturing processes, where efficiency and profitability are paramount, the Manufacturing Enterprise Resource Planning (ERP) system serves as your guiding beacon.
But with many options available, selecting the right fit can feel overwhelming. This guide provides a strategic framework to navigate the maze and identify the perfect Manufacturing ERP for your unique business needs.
DETERMINE YOUR REQUIREMENTS
Before you start comparing features, take the time to understand your specific needs. Here’s a roadmap to get you started:
- Industry Specificity
Not all ERPs are created equal. Identify solutions that cater to the nuances of your industry. A discrete manufacturer of aerospace components requires a different set of functionalities compared to a food and beverage producer. Seek an ERP with industry-specific workflows and prebuilt compliance features, saving you time and customization costs. - Production Processes
Analyze your core production processes. Do you operate under a Make-to-Order (MTO), Make-to-Stock (MTS), or a hybrid model? Ensure the chosen ERP offers functionalities that seamlessly integrate with your production flow, such as configurators for MTO or Advanced Planning and Scheduling (APS) for MTS environments. Consider the potential for future growth and choose an ERP that can adapt to evolving production models.
-
Data Landscape
Evaluate your current data infrastructure. How much data do you generate, and how will it grow in the future? Select an ERP that can handle your data volume efficiently without compromising performance. Furthermore, assess the need for integration with existing systems like CRM or CAD software. Look for an ERP with open APIs to facilitate seamless data exchange across your entire business ecosystem.
GO BEYOND THE FEATURES
While feature lists are important, delve deeper to discover the true value proposition of an ERP solution. Here’s what to consider:
- Vendor reputation and stability
Choose a vendor with a proven track record of success in implementing software used in the manufacturing industry and company size range. Research their customer service reputation, product development roadmap, and financial stability. You’re selecting a long-term partner, not just software for manufacturers. - Total Cost of Ownership (TCO)
Look beyond the purchase price. Factor in implementation costs, ongoing maintenance fees, training expenses, and potential hidden charges. Seek a vendor with transparent pricing structures and a willingness to work within your budget. - Implementation expertise
Implementing an ERP can be complex. Choose a vendor with a team of experienced consultants who understand your industry and can guide you through a smooth implementation process. Prioritize vendors who offer comprehensive training programs to ensure user adoption and maximize the ERP’s benefits.
INDUSTRY 4.0 CAPABILITIES
Manufacturing is on the verge of a transformative era—Industry 4.0. This revolution is defined by the integration of advanced technologies like Artificial Intelligence (AI), Machine Learning (ML), and the Internet of Things (IoT) into production processes.
A forward-thinking Manufacturing ERP should be equipped to embrace these advancements to stay ahead of the curve.
- Real-time analytics: Gain deeper insights from your production data than ever before. Leverage real-time analytics to identify trends, optimize production processes, and make data-driven decisions for continuous improvement. Advanced analytics can uncover hidden patterns and correlations within your data, leading to more informed decisions.
- Predictive maintenance: Move from reactive to proactive maintenance and minimize downtime. Machine learning functionalities within the ERP can analyze equipment data and predict potential failures with increased accuracy. Predictive maintenance allows you to schedule maintenance proactively, reducing the risk of unexpected disruptions and production delays.
- Enhanced quality control: Maintain consistent product quality. The ERP can integrate with AI-powered quality control systems that analyze inspection data and identify potential quality issues early in the production process. This allows for corrective actions to be taken promptly, minimizing the risk of defective products reaching customers and ensuring adherence to quality standards.
- Industrial automation integration: Connect your ERP to the shop floor seamlessly. Advanced ERPs can integrate with industrial automation systems, enabling real-time data exchange between machines and the ERP. Leveraging machine learning algorithms within the system allows you to optimize production processes based on real-time data from the shop floor, fostering a more automated and efficient production environment.
By seeking an ERP solution equipped with these Industry 4.0 capabilities, you position your manufacturing business to thrive in the dynamic landscape of the future.
By embracing enterprise resource planning, you can weave a tapestry of streamlined operations, informed decision-making, and sustained growth. However, the journey towards Manufacturing ERP software adoption requires a discerning eye, a forward-thinking mindset, and a committed approach.
If you are yet to embark on this transformative journey, the time is now. Don’t just observe the tide of Industry 4.0; be an active participant. Embrace the potential of ERP, and let it be the digital rudder steering your manufacturing business towards uncharted territories of success.
MORE ON MANUFACTURING ERP
DO YOU WANT TO KNOW MORE?
Request your personalized demo and find out how our ERP solutions can help support your business growth.